Simplified Order Picking Strategies: Handling Product Mix and Quantity Variability
(ii) Simple plans for simplifying the picking of orders that vary by product mix (a) and quantity (b)
(a) Addressing Variance in Product Mix
Orders for SKUs to be picked are received, then converted into quantity-based picking lists, wherein each list reports the number of a single SKU. When the picked SKUs are collected, the customer’s order is then assembled. The following diagram shows the three steps
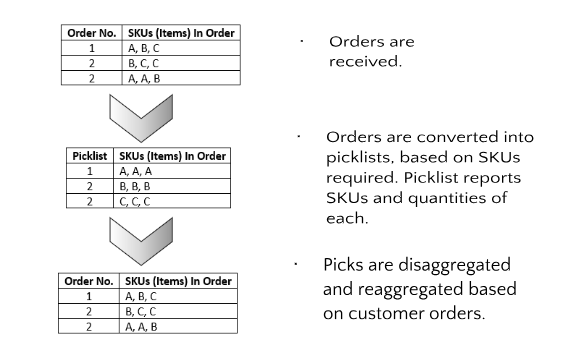
(b) Addressing Variance in Product Quantity
Variance in the quantity of goods ordered also represents a challenge for picking efficiency. A simple way of quantity variance management is achieved by use of aggregated, timed picks. Aggregated picks are quicker to perform due to their containing only similar or the same goods, and are in this way comparable to the method proposed for the management of variety in product mix (see above). Quantity variance can be managed using averaged historical figures that describe the quantities received, whether they be totals for mixed SKUs or single SKUs.
The table below shows how data on the quantities of product received in particular timeframes can be used to schedule and minimize picks to two per day. This method is suitable for demand patterns that indicate predictability. Other ways of pick smoothing include picking in readiness for planned demand interventions, such as campaigns, product launches, and discounts.
Picking orders (picklist creation) can also be based on zones or aisles. In the example below, four orders containing a variety of products (SKU) are received. (In this example, each order is for one customer). See the following table.
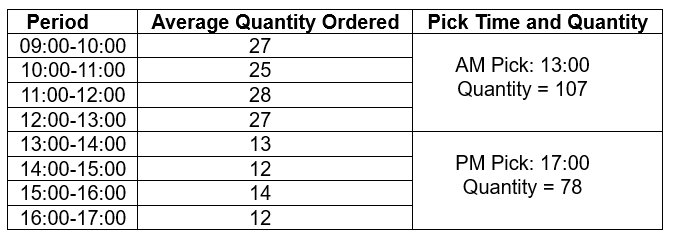
Orders Received for Picking (Conversion to Picklists)
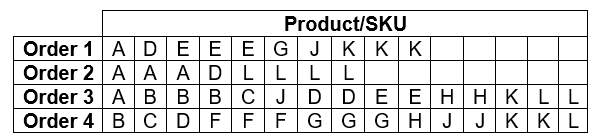
In this example, the warehouse has a fixed layout, in which goods (SKUs) are grouped for storage on particular aisles. The following table shows which items are located for storage in which aisles.
Aisle of Location of Products/SKUs
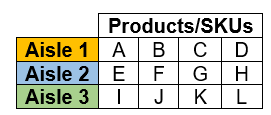
To simplify the picking process, the customer’s order is disaggregated. Picking lists are created on the basis of which aisles in the warehouse the SKUs in the customer order are stored. In the following tables, colour coding shows how the customer’s orders are split and reassembled as aisle-exclusive picklists.
Orders Received for Picking: SKUs Coded by Aisle of Location
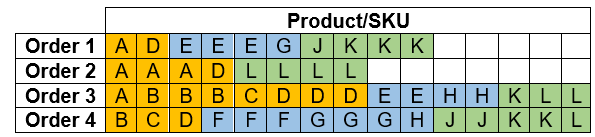
With the aisle-based picklist thus produced, the picker needs only visit one aisle to complete the pick. The table below shows a simple picklist format that should expedite the pick process.
Picklists: SKUs Aggregated by Aisle

Notes
This method (b) is likely more efficient than picking by customer order, since in a customer order, variety maybe high (although this will vary according to what is being retailed), meaning the picking distance/time will be as random as the content of the order. However, the method proposed here has its problems. The picked SKUs will have to be disaggregated at a point close to despatch, and then reaggregated so that it can be shipped as a consolidated order to the customer. There is also the problem of staff downtime while orders build during both periods of the day. Operations planning will have to account for this and allocate staff to other tasks while orders are building.
These methods are all picker-to-goods, and can be made more efficient by sequencing the picklist to apply U-path or Snake-path routing. However, both methods described here assume that mixed orders contain no items for urgent dispatch. Items so marked may not be suitable for pick with these methods, since both require periods of time for orders to aggregate.