Analysing Marketing Logistics
Analysis of the Marketability of the Current Logistics Chain
The following diagram is an approximate illustration of a consumer electronics source-to-UK-customer supply chain.
Mapping a supply chain allows managers to understand the durations, directions, costs, complexities, and constraints of its flows. The principle underlying logistics management is competitive advantage through logistical efficiency. Management of the logistical activities within a supply chain typically begins with a mapping of the major flows. Mapping can thus be considered the first step toward achieving/increasing competitive advantage through improvement/simplification of logistical activities.
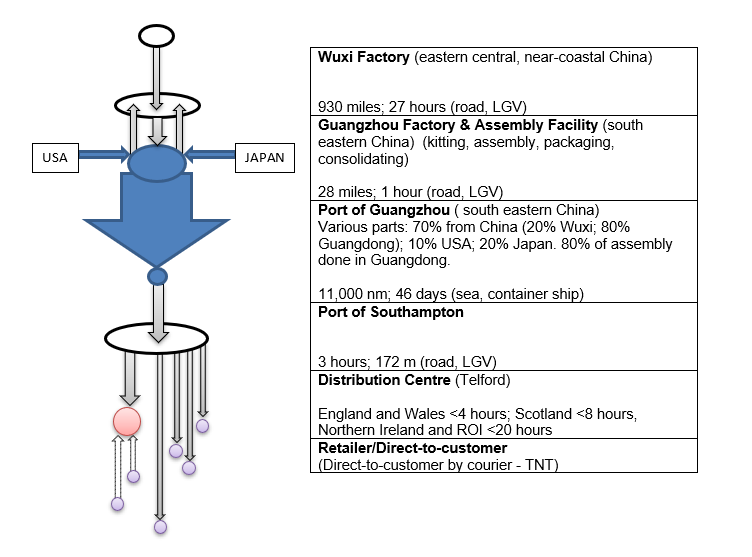
Various parts: 70% from China (20% Wuxi; 80% Guangdong); 10% USA; 20% Japan.
80% of assembly done in Guangdong
A Marketing Plan
A marketing plan that is currently receiving feasibility study involves multimodal transportation from Southampton to the Telford Distribution Centre. Currently, freight is unpacked from containers at dock and then transported by road to Telford. Costs are incurred by the unloading and reloading phase. Dockside storage must be paid for if collection cannot be immediate. A potentially superior plan would involve moving containers directly from ship to rail. The containers would arrive at TIRP (Telford International Retail Park) and then be transported to Telford DC by truck. The time by truck from Southampton to Telford is shorter by approximately one hour than the time by rail. Also, the rail freight option requires transfer to truck at TIRP.
The cost of cheaper-by-volume transport by rail will be weighed against the faster time and convenience of transport by truck (the last mile advantage of truck transport is commercially significant). The inclusion of another modality (rail) incurs a time/cost and coordination trade off and an extra set of potential failure points.
The break bulk point is also critical and so demands evaluation. A Southampton bulk break is expensive but would allow faster and cheaper distribution to retailers in southern England and Wales – if a suitable information system could facilitate the sort economically. This would reduce the space required for storage at the Telford DC, because approximately 40% of items are ultimately dispatched to southern England. Currently, sort and storage occurs at the Telford DC. A Midlands bulk break captures scales of economy (trucks can be loaded to capacity) and the storage facility buffers against interruption, but items bound for southern retailers are a time and cost duplicator.
Forward of the Telford DC, fleet costs could be saved if incidence of irregular, low-volume orders dispatched directly to customers could be reduced and independent couriers used instead of 3PL couriers. Direct trucking of bulk from port to retailer would be ideal, but for this to be feasible, a capable sort system would have to be available. If items could be sorted at the dock (split down from containers to pallets to units), transport and storage time and costs could be reduced.
A 3PL with nationwide regional short-term storage/cross docking facilities could offer a solution. The currently centralized model is suboptimal. Lead times are not a critical issue, but rising fuel costs are being reflected in pricing, which may be proving deleterious to sales. Our products are competing in a saturated market in which bigger companies with wider product ranges and higher sales volumes of competing products (e.g. Hewlett Packard’s printer division) are able to leverage advantages of scale. Hence increasing price is the least desirable option. Reducing the running costs of internal processes, such as logistics, is a better solution.
A 3PL with rail freight capability would likely lower transportation costs. Use of diffusely located 3PL storage/cross docking (groupage/consolidation) facilities could further reduce logistics expenditure. Collection from dock to third-party DC for ASAP dispatch to retailers or direct-to-customer dispatch would be ideal, if the savings incurred by the outsourcing outweighed the costs of the current system and the 3PL was equipped to cope with capacity fluctuation.