Analysing Logistics 2: Process Outline Modelling
Modelling/diagramming helps the analyst understand what happens in a logistics process, where, and in what sequence. Diagrams can be very simple, showing only the most basic elements, or they can be highly detailed, giving lead times, names of actors, indicators of volume and direction of goods, and even costs associated with different activities. The analyst may be a stranger to logistics systems and want a basic understanding of the company’s flows, since these will give the approximate locations of failure. When these are known, the analysis can then focus on these areas and expose the root causes (we hope).
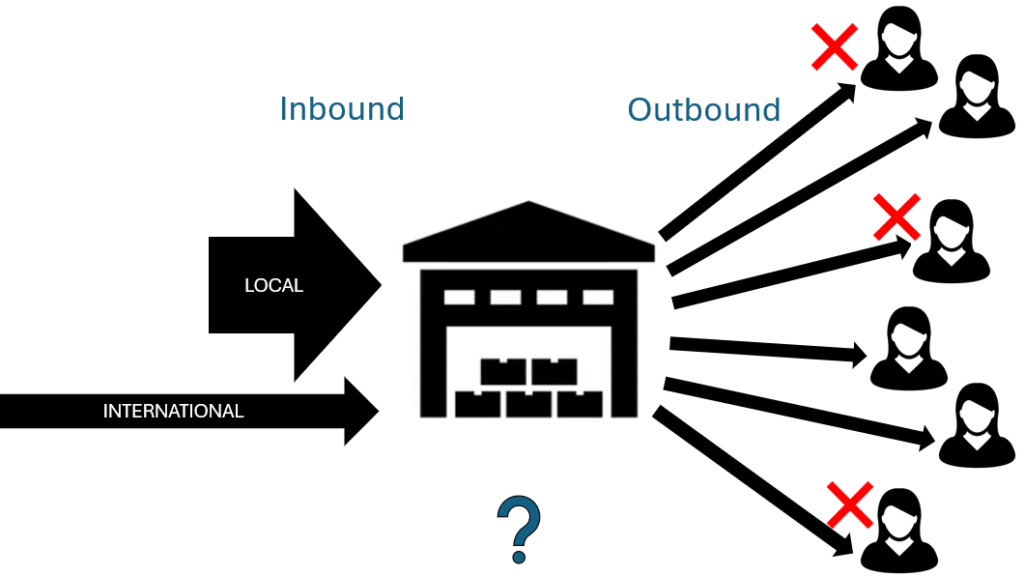
Even in this most basic of diagrams, we can see at a glance that 50% of our customers are not receiving their orders as required, and the point of failure appears to be at or after the DC (Distribution Centre). We know this because only inbound product that passes Quality Control at the DC is placed into inventory and subsequenty dispatched. From our data on returns at the point of inbound QC, we know that very few goods are returned to the suppliers due to fault. Fulfilment is therefore failing due to problems inside the DC, at dispatch, or post-dispatch.
This shows us that the majority of product is sourced locally, and only a small portion comes from overseas suppliers. Product is shipped into one central Distribution Centre. There being no indicator of reverse logistics at the inbound phase suggests very few products (actually only 12%) fail Quality Control at receipting. The red crosses next to the customer indicate failed orders, however. We know that distribution is more likely causative of the non-fulfilment of order than problems with the product. For this reason, we will look more closely at what is occurring post-receipting and during despatch.